
Device overview
The smelting process of laterite nickel ore is used to reduce ferronickel. The main raw material is laterite nickel ore. The reducing agent can use cheap coal, peat or medium coal. The process steps mainly include material preheating, reduction melting process, and sorting and refining. When the equipment is running, the main drive motor transmits power to the open gear device through the main reducer to drive the kiln body to rotate, and the laterite nickel ore enters the rotary kiln from the kiln tail for calcination. Due to the inclination and slow rotation of the cylinder, the material rolls in the circumferential direction and moves in the axial direction to continue its technological process. Then, the raw clinker enters the cooler for cooling through the kiln head cover. The fuel is injected into the kiln from the kiln head, and the waste gas produced by combustion is exchanged with the material, and then exported from the kiln tail.

The use of laterite nickel ore
Metal nickel has very good magnetic properties and plasticity, and at the same time has good corrosion resistance and ductility . It is mainly used for alloy doping and metal catalysts, especially as a catalyst for hydrogenation . Nickel is plated on other metals It can prevent the oxidation and corrosion of metals on the surface . Nickel is mainly used in alloys to make stainless steel and other anti-corrosion materials. The alloy with higher nickel content has stronger anti-corrosion ability . It is also widely used in chemical vessels for special purposes, industrial batteries, green glass and the preparation of nickel compounds.
Equipment composition
The laterite nickel ore rotary kiln is composed of a cylinder body, a wheel belt, a supporting wheel, a blocking wheel, a transmission device, and a kiln head and kiln tail sealing device.

Rotary kiln process of laterite nickel ore
Preparation of ore treatment and reducing agent - calcination in rotary kiln - smelting in submerged arc furnace with hot charging - out-of-furnace desulfurization of crude ferronickel - removal of impurities such as silicon, phosphorus, carbon, sulfur and manganese in converter - - Refined nickel molten iron ingots, additionally need to build a workshop for recycling and utilizing iron and nickel in converter slag.
( 1 ) Preparation of ore processing and reducing agent
After the ore is transported into the raw material yard , it is crushed, neutralized and mixed, and a reducing agent is added to the rotary kiln. Some factories pre-dry the charge before entering the rotary kiln, and some increase the pelletizing process of the charge. The ratio of the charge is important, which plays a decisive role in preventing the rotary kiln from ringing ( the charge sticks to the furnace lining ) , controlling the electrical conductivity of the charge, and separating the slag and metals ( nickel, iron ) in the submerged arc furnace .
( 2 ) Rotary kiln calcination
The working area of the rotary kiln can be divided into three sections, namely drying section, heating section and roasting section. In the rotary kiln, the ore is roasted and dehydrated, and the weight is reduced by about 30 %. At the same time, the nickel oxide and part of the iron are reduced by the reducing agent in the charge. There is a sealed discharge device at the discharge end of the rotary kiln, and the nickel slag is sent to the heat-insulated feeding bunker of the submerged arc furnace at a temperature of 600-900 °C under heat insulation, and then passes through a sealed material . The tubular distribution device is evenly distributed into the submerged arc furnace. Rotary kilns have different ratios of diameter and length depending on how the charge is processed. The burner structure of the rotary kiln is important, and the length and stiffness of the flame can be adjusted effectively to ensure that the temperature of the three working areas in the furnace is within the range of process requirements. In addition, it is necessary to fully consider the use of the flue gas of the rotary kiln to dry the charge to save energy.
(3) Hot charging into submerged arc furnace for smelting
After the material from the rotary kiln is weighed, it is charged into the submerged arc furnace in a hot state. The charging system of the submerged arc furnace needs to adapt to the needs of hot charging . Hot charging is very important. In addition to recovering physical heat, it is also necessary to ensure that the material is not subject to secondary oxidation during the transfer process. For environmental protection, industrial hygiene, dust recovery, and gas recovery, the submerged arc furnace is sealed. In the submerged arc furnace, through the electric arc smelting , the crude nickel iron and the electric furnace slag are separated, and the reducing gas containing 75 % CO is produced at the same time. 30 %. According to different raw materials, 1 ton of raw ore can be calcined in a rotary kiln to obtain ~0.650 ~ 700 kg of nickel slag, and 110 ~ 150 kg of crude nickel can be obtained after smelting in a submerged arc furnace . iron. The nickel content in crude ferronickel is generally 10 % to 18 %.
( 4 ) Refining of crude ferronickel
In the process of tapping iron into the molten iron in the submerged arc furnace, soda ash is added to the ladle at a rate of 5-15 kg per ton of molten iron , and the sulfur in the molten iron can be reduced . 0 l 5 %~0 . 08 %. It is also possible to spray granular magnesium into the molten iron ladle after tapping, which requires a special evaporator to spray granular magnesium into the ladle 1 . At a depth of about 0 m , this process can reduce the sulfur in molten iron by No. 0 l 5 % or less.
The slag above the crude nickel molten iron is removed, and it is mixed into an acid converter, and the silicon is oxidized by blowing oxygen. In order to control the temperature of the molten pool not too high, metal waste or nickel-containing waste is added to the furnace.
The desiliconized nickel molten iron is then mixed into an alkaline converter, where carbon, phosphorus and part of iron in the nickel molten iron are removed. Limestone is added to the converter during the smelting process. Limestone can be replaced by lime when there is sufficient nickel-containing waste. The molten nickel iron from the alkaline converter has met the requirements of the commercial nickel iron standard and can be sold as commercial nickel iron. In addition, the two-step refining process for crude ferronickel is to change the acid converter to an alkaline converter, and adopt a new process to achieve desiliconization and desulfurization in the first converter. The molten nickel iron from the first converter enters the second basic converter for dephosphorization and decarburization. During the smelting process, lime and limestone are added to the furnace to ensure proper smelting temperature. Two-step refining can obtain qualified refined nickel molten iron.
Product Specifications ( m ) |
Kiln body size |
Motor power ( kw ) |
total weight ( t ) |
Remark |
||||
Diameter ( m ) |
length ( m ) |
Slope ( % ) |
Yield ( t/d ) |
Speed ( r/min ) |
||||
Φ 2.5 × 40 |
2.5 |
40 |
3.5 |
180 |
0.44-2.44 |
55 |
149.61 |
|
Φ 2.5 × 50 |
2.5 |
50 |
3 |
200 |
0.62-1.86 |
55 |
187.37 |
|
Φ 2.5 × 54 |
2.5 |
54 |
3.5 |
280 |
0.48-1.45 |
55 |
196.29 |
Out-of-kiln decomposition kiln |
Φ 2.7 × 42 |
2.7 |
42 |
3.5 |
320 |
0.10-1.52 |
55 |
198.5 |
------ |
Φ 2.8 × 44 |
2.8 |
44 |
3.5 |
450 |
0.437-2.18 |
55 |
201.58 |
Out-of-kiln decomposition kiln |
Φ 3.0 × 45 |
3 |
45 |
3.5 |
500 |
0.5-2.47 |
75 |
201.94 |
------ |
Φ 3.0 × 48 |
3 |
48 |
3.5 |
700 |
0.6-3.48 |
100 |
237 |
Out-of-kiln decomposition kiln |
Φ 3.0 × 60 |
3 |
60 |
3.5 |
800 |
0.3-2 |
100 |
310 |
------ |
Φ 3.2 × 50 |
3.5 |
50 |
4 |
1000 |
0.6-3 |
125 |
278 |
Out-of-kiln decomposition kiln |
Φ 3.3 × 52 |
3.3 |
52 |
3.5 |
1300 |
0.266-2.66 |
125 |
283 |
Preheating decomposition kiln |
Φ 3.5 × 54 |
3.5 |
54 |
3.5 |
1500 |
0.55-3.4 |
220 |
363 |
Preheating decomposition kiln |
Φ 3.6 × 70 |
3.6 |
70 |
3.5 |
1800 |
0.25-1.25 |
125 |
419 |
Preheating power kiln |
Φ 4.0 × 56 |
4 |
56 |
4 |
2300 |
0.41-4.07 |
315 |
456 |
Preheating decomposition kiln |
Φ 4.0 × 60 |
4 |
60 |
3.5 |
2500 |
0.396-3.96 |
315 |
510 |
Preheating decomposition kiln |
Φ 4.2 × 60 |
4.2 |
60 |
4 |
2750 |
0.41-4.07 |
375 |
633 |
Preheating decomposition kiln |
Φ 4.3 × 60 |
4.3 |
60 |
3.5 |
3200 |
0.396-3.96 |
375 |
583 |
Preheating decomposition kiln |
Φ 4.5 × 66 |
4.5 |
66 |
3.5 |
4000 |
0.41-4.1 |
560 |
710.4 |
Preheating decomposition kiln |
Φ 4.7 × 74 |
4.7 |
74 |
4 |
4500 |
0.35-4 |
630 |
849 |
Preheating decomposition kiln |
Φ 4.8 × 74 |
4.8 |
74 |
4 |
5000 |
0.396-3.96 |
630 |
899 |
Preheating decomposition kiln |
Φ 5.0 × 74 |
5 |
74 |
4 |
6000 |
0.35-4 |
710 |
944 |
Preheating decomposition kiln |
Φ 5.6 × 87 |
5.6 |
87 |
4 |
8000 |
Max4.23 |
800 |
1265 |
Preheating decomposition kiln |
Φ 6.0 × 95 |
6 |
95 |
4 |
10000 |
Max5 |
950 × 2 |
1659 |
Preheating decomposition kiln |
Shandong Linyi **** Co., Ltd. Laterite Nickel Mine Rotary KilnΦ4.85×75m
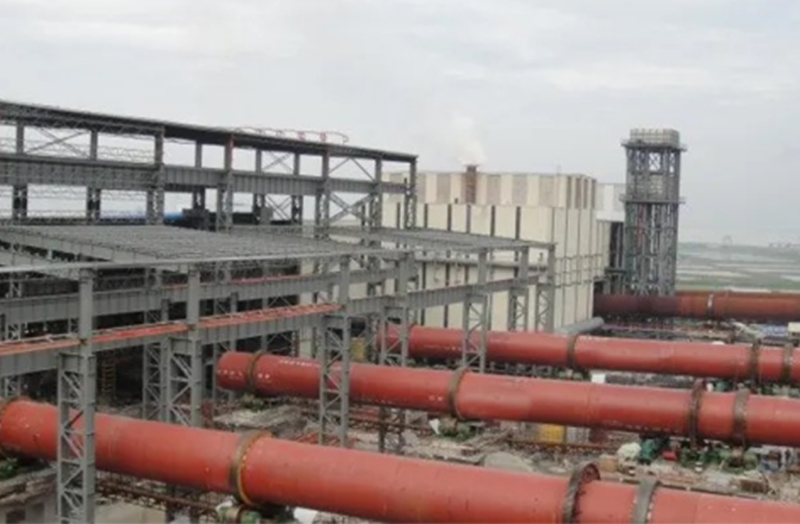
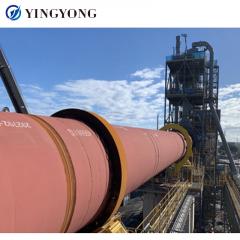
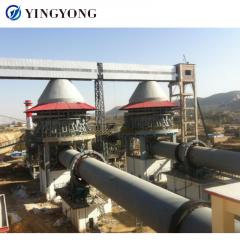
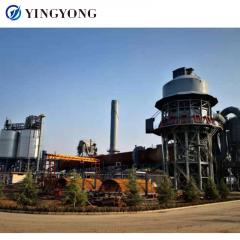