
Equipment composition
The ceramsite rotary kiln is composed of shell, tyre, support roller, thrust roller, transmission device and sealing device at the kiln head and kiln tail.

The use of ceramsite
Ceramsite sand is a kind of ceramic particle product with high fracturing strength. It is mainly used for downhole support in oilfields to increase the production of oil and natural gas. It is an environmentally friendly product. This product is made of high-quality bauxite, coal and other raw materials, and is sintered with ceramics. It is a substitute for medium and low strength proppants such as natural quartz sand, glass balls, and metal balls. It has a good effect on increasing oil and natural gas production.
Types of ceramsite

Equipment composition
The ceramsite rotary kiln is composed of shell, tyre, support roller, thrust roller, transmission device and sealing device at the kiln head and kiln tail.
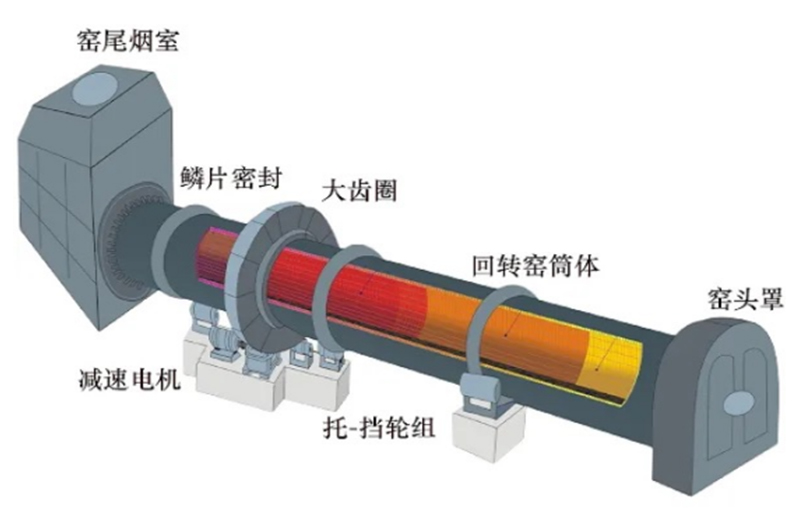
Ceramsite Rotary Kiln Technology
The production process of petroleum proppant ceramsite sand is briefly described below:
1. Crushing:
The mined bauxite is generally about 300~500mm in size and contains a small amount of water. Generally, a secondary crushing system composed of jaw crusher and hammer crusher is used, and its particle size is controlled to be ≤8mm.After entering the factory, the bauxite can be stacked separately according to the different grades. When used, use it according to the indicator.Manganese (Mn) is usually added during the production of ceramsite to reduce the sintering temperature and dye the product dark. At present, most domestic manufacturers use low-grade (~50%) manganese ore or manganese ash as the source of manganese.
2. Batching:
Several materials such as bauxite, manganese powder, and return material are transported to their respective material warehouses, and a speed-adjusting belt scale is set under the warehouse to realize automatic batching and measurement of materials.
3. Grinding:
Generally, a ball mill for drying and grinding is used, and a high-efficiency powder separator is used to form a closed-circuit system. This grinding efficiency is high.
The hot air for drying materials can come from the waste gas of the rotary kiln, so as to utilize the waste heat; a special hot air furnace can also be set up. Jiangsu Pengfei Group Co., Ltd. broke through the original frame and replaced the ball mill with a vertical mill. It has achieved great success in Yunnan Heqing Xinke Aluminum Co., Ltd., the HRM2200 vertical mill, the ratio requirement is above 450m2/g, and the output reaches 25T/h .Aluminum vanadium soil vertical mill has great potential.
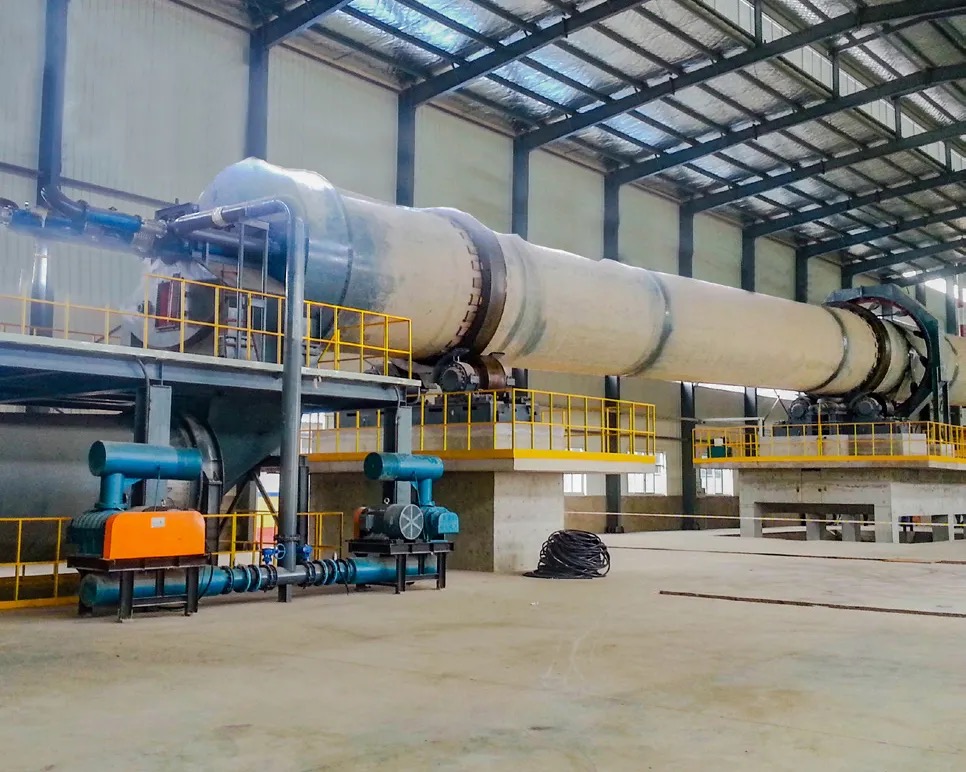
4. Ball making:
The milled raw meal is stored in the raw meal warehouse. Generally, 2~3 warehouses are set up, which can be discharged individually or with multiple warehouses.
The raw meal powder is fed into a small silo, and a screw metering device or a speed-adjusting belt weighing device is installed under the silo to measure the amount of raw meal. The raw meal enters the disc ball making machine. At the same time, the flow meter can be used to measure the amount of water, and the water is sprayed into the disc ball making machine by the pipeline pump. During the rotation of the ball making machine, pellets of various particle sizes can be made. After the material balls are out of the tray, they are sent to the screening device by the belt conveyor, the qualified ones enter the rotary kiln, and the oversized ones are returned to the raw material grinding process. According to the output of different kilns, it can be equipped with different numbers of disc-type ball making machines (ball-forming discs).
The ball making system has a high degree of automation and a continuous process. After being equipped with a bag filter, it can achieve the job dust compliance and purify the job environment.
5. Calcination:
The pellets enter the rotary kiln with a certain inclination for calcination. With the rotation of the rotary kiln, the pellets roll toward the kiln head, and at the same time, the coal powder is injected into the kiln from the kiln head for combustion, and the pellets are calcined in the rotary kiln to the strength Very high ceramsite sand.
The pulverized coal burner can use a single air duct coal injection pipe, which is simple and reliable, and has a high primary air volume; it can also use a multi-air duct burner, and the primary air volume can be reduced to 8% of the air volume required for pulverized coal combustion, which improves the secondary kiln entry. Air volume, energy saving effect is remarkable. The multi-channel burner is divided into outer axial flow air, coal air, inner axial flow air, etc. The flame shape is very easy to adjust.
The measurement of pulverized coal can be carried out by a rotor-type weighing scale or a Coriolis force scale, which can precisely control the amount of coal and stabilize the thermal system in the kiln.
6. Pulverized coal preparation:
The pulverized coal can be prepared by ball mill or vertical mill, and hot air can be extracted from the kiln hood to dry the pulverized coal. The fineness of the pulverized coal can be adjusted arbitrarily by using the dynamic separator, which provides conditions for the full combustion of the pulverized coal.
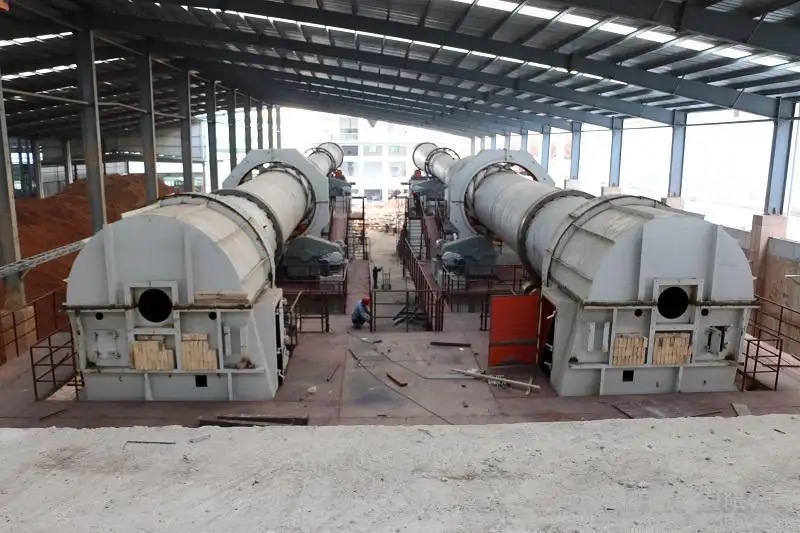
7. Finished product cooling:
The cooling of ceramsite sand generally uses a rotary cooler, which is simple and reliable. The secondary air of the cooler is completely fed into the kiln, and the use of multi-channel burners can save a lot of energy. The temperature of the ceramsite sand coming out of the cooler is very low and can be picked up by hand.
8. Screening:
The ceramsite sand from the cooler can be directly transported to the multi-stage vibrating screen, and divided into multiple particle size grades as required.
Specifications of ceramsite sand
Type I 0.45-0.9mm (20-40 mesh) high strength and medium density
Type II 0.9-1.25mm (16-20 mesh) high strength and medium density
Type III 1.0-1.70mm (12-18 mesh) high strength and medium density
Type IV 0.224-0.65mm (40 mesh-60 mesh) high strength and medium density
序号 No. |
规格(m) Specification |
生产能力 Capacity |
斜度 Slope(%) |
筒体转速 Shell speed (r/min) |
减速机 Gearbox |
电动机 Motor |
|||
时产量 Per hour (m3/h) |
年产量 Anual (10000 m3/a) |
型号 Model |
功率 Power(kW) |
||||||
1 |
预热窑 preheating kiln |
φ1.25×18 |
2.95~3.94 |
1.8~2.4 |
4 |
1.0~5.0 |
ZQ500 |
YCT225-4A |
11 |
焙烧窑 calcining kiln |
φ1.6×14 |
1.0~5.0 |
ZQ650 |
YCT225-4B |
15 |
||||
2 |
预热窑 preheating kiln |
φ1.55×20 |
4.36~5.81 |
2.67~3.5 |
4 |
1.0~5.0 |
ZQ650 |
YCT250-4A |
18.5 |
焙烧窑 calcining kiln |
φ1.9×16 |
1.0~5.0 |
ZQ750 |
YCT250-4B |
22 |
||||
3 |
预热窑 preheating kiln |
φ1.8×22 |
5.9~7.87 |
13.61~4.8 |
4 |
1.0~5.0 |
ZQ750 |
YCT250-4B |
22 |
焙烧窑 calcining kiln |
φ2.2×18 |
1.0~5.0 |
ZQ750 |
YCT250-4B |
22 |
||||
4 |
预热窑 preheating kiln |
φ2.0×24 |
7.42~9.88 |
4.54~6 |
4 |
1.0~5.0 |
ZSY224 |
YCT280-4B |
30 |
焙烧窑 calcining kiln |
φ2.5×20 |
1.0~5.0 |
ZSY224 |
YCT315-4A |
37 |
||||
5 |
预热窑 preheating kiln |
φ3.0×20- φ2.5×12 |
9.5~17.51 |
8.04~10.7 |
4 |
1.0~5.0 |
ZS1450 |
YCT355-4B |
75 |
焙烧窑 calcining kiln |
φ3.0×22 |
1.0~5.0 |
ZS1250 |
YCT355-4A |
55 |
||||
6 |
预热窑 preheating kiln |
φ3.2×20- φ2.8×14 |
13.9~16.2 |
10.0~11.5 |
4 |
1.0~5.0 |
ZS1450 |
YCT355-4A |
55 |
焙烧窑 calcining kiln |
φ3.0×22 |
1.0~5.0 |
ZS1250 |
YCT355-4A |
55 |
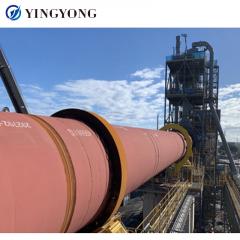
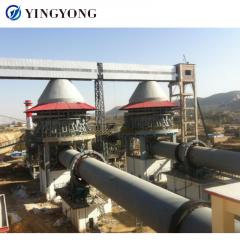
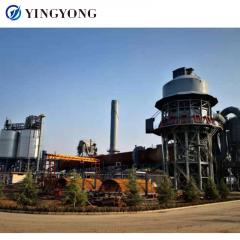