

The mill is a kind of equipment that combines drying, grinding, and powder selection as a kind of milling equipment. It is widely used in the fields of coal chemical industry, thermal power, steel and non-metallic mineral grinding.
(1) Coal Mill: Coal is an inflammable and explosive mineral. The mill can be used for the grinding of materials such as bituminous coal, anthracite, lignite, petroleum coke, coke, and asphalt. It is a coal-fired power plant and coal chemical industry. The preferred device.
(2) Non-metallic mineral grinding: It is applicable to industrial milling fields such as limestone, lime, barite, talc, gypsum, cement raw material, slag, cement, etc.
The HP high-efficiency vertical pulverizer is mainly composed of the following components (see Figure 1), falling coal pipe, pulverized coal export gate valve, dynamic separator device, spring-loaded device, high-efficiency roller device, bowl-grinding device, and stone coal Collection devices, transmissions, bases, housings, etc.
The dynamic separator is an efficient and energy-saving powder selection device. The roller device is used to grind and crush the material. The grinding device is fixed on the output shaft of the speed reducer and is the area where the roller rolls the material. A spring-loaded device is a component that provides grinding pressure to a grinding roller and provides sufficient pressure to the grinding roller to crush the material.
System process
1. Single pulse dust collector open circuit system
The raw materials of this system are lifted to the required height through the bucket elevator. After the iron is removed, the materials are put into the middle warehouse. Under the pre-determined amount of feed, the closed dosing feeder weighs the materials and feeds the materials. Into the vertical mill for grinding. Vertical mill grinding qualified products are collected by a box-type pulse bag filter to reduce the number of equipment and simplify the system configuration. After the product is collected, it is fed into the finished silo through a bucket elevator using a screw feeder. This system is characterized by its simple structure, little equipment used, low equipment investment, no drying heat source, low operating cost, relatively dry materials (<4% moisture), and no need for drying operations in the system.
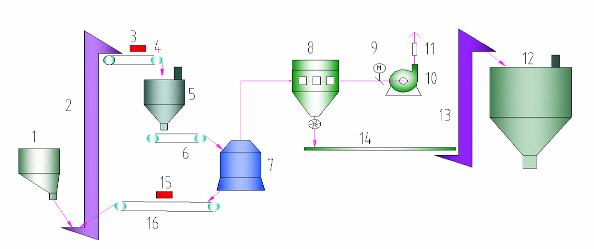
1 silo 2 Bucket elevator 3 Iron remover 4 Belt conveyor 5 silo 6 Dosing feeder 7Vertical mill 8 Pulse bag filter 9Air valve 10 Fan 11silencer 12Silo 13 Bucket elevator 14 Screw conveyor 15 Iron remover 16 Belt conveyor
2. Single pulse dust collector open circuit system
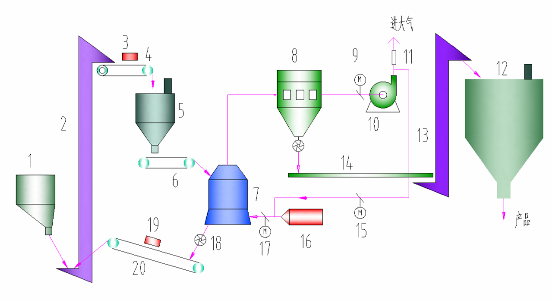
1 silo 2 Bucket elevator 3 Iron remover 4 Belt conveyor 5 silo 6 Dosing feeder 7 Vertical mill 8 Pulse bag filter 9 Air valve 10 Fan 11 silencer 12 Silo 13 Bucket elevator 14 Screw conveyor 15 Hot air control valve 16 Hot stove 17 Hot air control valve 18 Wind lock discharge valve 19 Iron remover 20 Belt conveyor
The motor drives the disc to rotate through the speed reducer so that the material falls from the feed inlet to the center of the disc and the hot air enters the mill from the intake port. With the rotation of the turntable, under the action of centrifugal force, the material is brought up to the edge of the grinding disk by the high-speed air circulation of the wind ring, and the large particles are directly dropped onto the grinding disk and re-grinded. The material in the air flow enters the upper separator when rotating the rotor. Under the action, the coarse powder falls from the cone to the grinding disc and is reground. The qualified fine powder is milled together with the air flow and collected by the dust collection device. It is the product, and the moisture-containing material is dried during the contact with the hot gas. By adjusting the hot air temperature, it can meet the requirements of different humidity materials and reach all the required product moisture. By adjusting the separator, the required fineness of different products can be achieved.
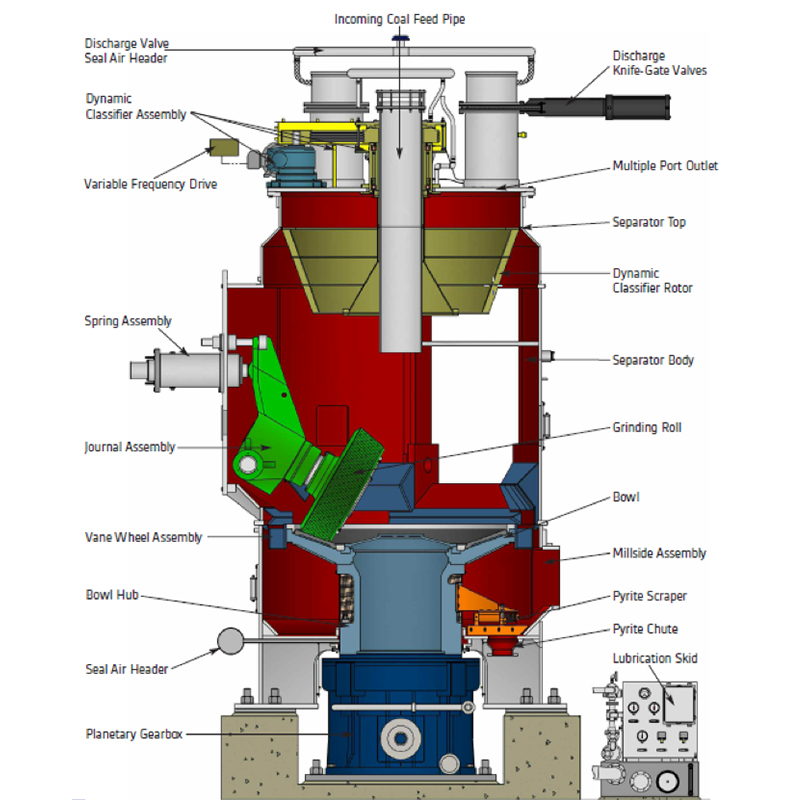
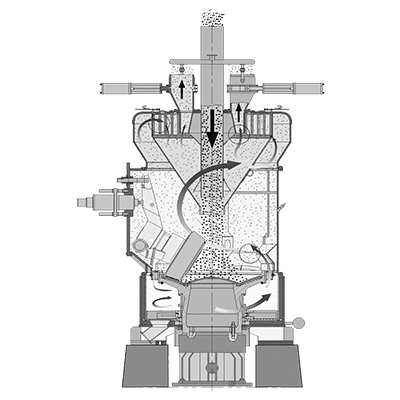
型号 model |
磨盘直径 Disc diameter (mm) |
磨辊直径Roller diameter (mm) |
入磨粒度 input (mm) |
产能 Capacity (t/h) |
风量 Air volume (t/h) |
磨碗转速 Disc speed (r/min) |
功率 Power (Kw) |
重量 Weight (T) |
HP683 |
1900 |
1100 |
≤38 |
31.7 |
36.1 |
45.2 |
225~260 |
75 |
HP703 |
34.7 |
39.5 |
||||||
HP723 |
37.8 |
42.7 |
||||||
HP743 |
41.1 |
46.5 |
||||||
HP763 |
2100 |
1200 |
44.6 |
52.4 |
41.3 |
260~300 |
90 |
|
HP783 |
48.2 |
54.4 |
||||||
HP803 |
52.4 |
59.3 |
||||||
HP823 |
2200 |
1300 |
56.0 |
65.3 |
38.4 |
345~400 |
115 |
|
HP843 |
59.9 |
68 |
||||||
HP863 |
63.5 |
72.1 |
||||||
HP883 |
2400 |
1400 |
67.3 |
76.7 |
35 |
400~450 |
135 |
|
HP903 |
71.3 |
83 |
||||||
HP923 |
75.1 |
85.5 |
||||||
HP943 |
79.1 |
89.8 |
||||||
HP963 |
2600 |
1500 |
82.6 |
94.7 |
33 |
450~520 |
140 |
|
HP983 |
86.2 |
98 |
||||||
HP1003 |
89.8 |
102.1 |
||||||
HP1023 |
2800 |
1600 |
95.8 |
108.9 |
30 |
520~700 |
160 |
|
HP1043 |
101.8 |
115.7 |
||||||
HP1063 |
110.7 |
125.9 |
||||||
HP1103 |
119.7 |
136.1 |
1.Small footprint, low investment costs
Due to the combination of crushing, drying, grinding and grading and conveying, the system is simple, the layout is compact, the area is about 50% of the ball mill system, and it can be arranged in the open air, so it can greatly reduce the investment cost.
Low operating costs
(1) Low energy consumption: The grinding roller directly grinds the grinding material on the grinding disc, which has low energy consumption and saves energy consumption of 30% to 40% compared with the ball milling system.
(2) Less wear: Because the grinding roller is not in direct contact with the grinding disc during work, and the grinding roller and the liner are made of high-quality materials, the service life is long and the wear is small.
(3) Long life: The roller roller sleeve is designed as a composite structure of cast steel and hardfacing. After the wear layer is worn, it can be repeated and the service life is extended 3-4 times.
2.Adjustable loading force, strong applicability, high milling efficiency
Through the spring or hydraulic pressure can increase the size of the grinding force, which can increase production, improve the efficiency of milling; at the same time there is a stopper device, but the material is milled to prevent accidental contact of the grinding ring Causes equipment vibration or even wear.
3.Strong drying capacity
4.Product quality is stable
residence time in the mill, it is easy to detect and control the product particle size and chemical composition, reduce repeated grinding, and stabilize product quality. The iron content in the product is very small, and the mechanical wear iron contained in it is easy to remove. When used to grind white or transparent materials, the product has high whiteness and cleanliness.
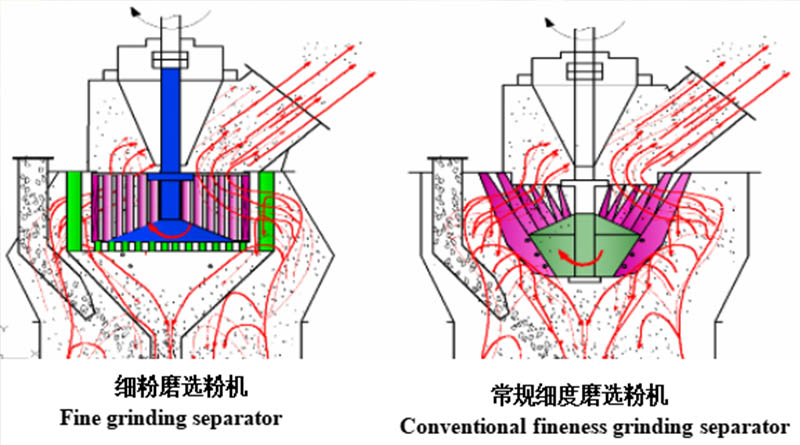
- 5.High selection accuracy
- According to the different particle size requirements of the finished products, the separators use cage separators (high-efficiency static and dynamic separators) and conical rotor separators (high-efficiency dynamic separators).
- 6.Easy to maintain
- By overhauling the cylinders, turning the booms, replacing the sleeves and linings is quick and easy, reducing downtime losses and saving labor costs.
- 7.Protect environment
- The vibration is small, the noise is low, and the equipment is totally sealed. The system works under negative pressure, there is no dust spill, the environment is clean, and it meets the national environmental protection requirements.
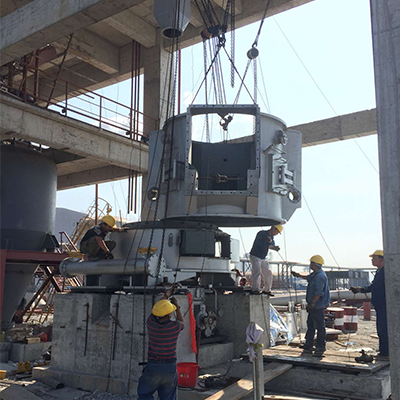
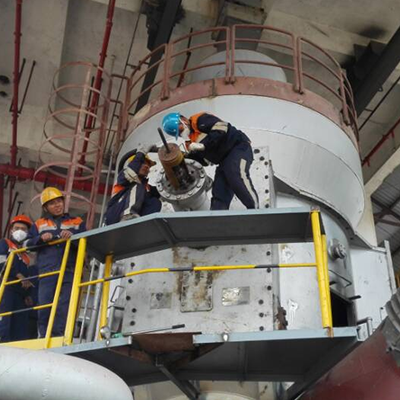
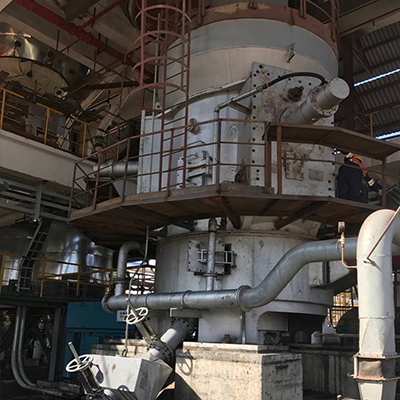
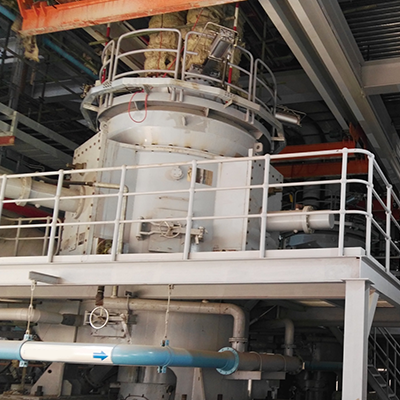
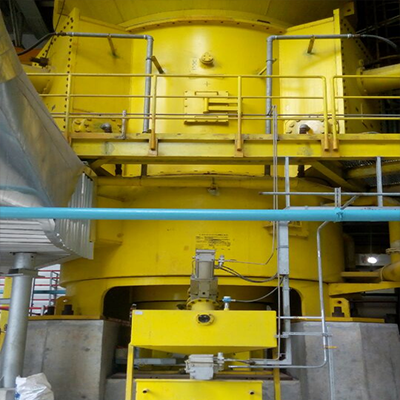

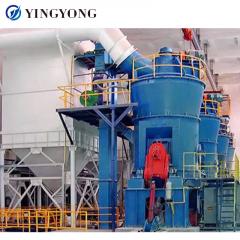
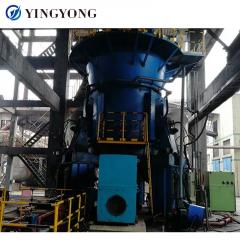
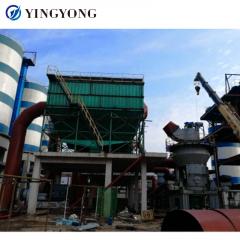