
Rotary kiln can be divided into cement kiln, metallurgical chemical kiln and lime kiln according to different materials. Cement kilns are mainly used for calcining cement clinker. There are two kinds of kilns: dry production and wet production. Metallurgical and chemical kilns are mainly used for magnetizing roasting of lean iron ore in metallurgical industry. Chromium and nickel-iron ore oxidation roasting; The high alumina vanadium ore and the clinker and aluminum hydroxide were roasted in the refractory factory; Chemical plants roasted chromium ore and chromium ore powder and other minerals. Lime-kiln (active lime-kiln) is used for calcining active lime and light calcined dolomite used in iron and steel works and ferroalloy factories.

A rotary kiln (rotary kiln) is a cylinder with a certain slope of 3 to 3.5%. The kiln's rotation promotes mixing of materials in the rotary kiln (rotary kiln). A large amount of heat is generated by the combustion of coal injection at the kiln head, which is transmitted to the materials by means of flame radiation, convection of hot air and conduction of kiln bricks (kiln skin). The e material moves forward in the kiln depending on the inclination of the kiln cylinder and the rotation of the kiln.
The cement rotary kiln operates at high temperature with heavy load and low speed. The maintenance of its accessories and the level of thermal control system are related to the safety and efficiency of rotary kiln operation. The maintenance of transmission device focuses on lubrication, running state, dynamic detection and meshing precision of big and small gears. The installation accuracy of the supporting device determines whether the rotary kiln can run safely and reliably. During the operation, attention should be paid to the rational control of the bearing capacity distribution of each gear supporting wheel, the layout of the supporting wheel, the pressure and time of the upstream and downstream of the hydraulic gear, the bearing force of the supporting wheel, and the gap between the belt and the backing plate. The quality of sealing device directly affects the thermal system and operating cost of rotary kiln. Strengthen the daily maintenance data analysis of rotary kiln, which is beneficial to the management of equipment.
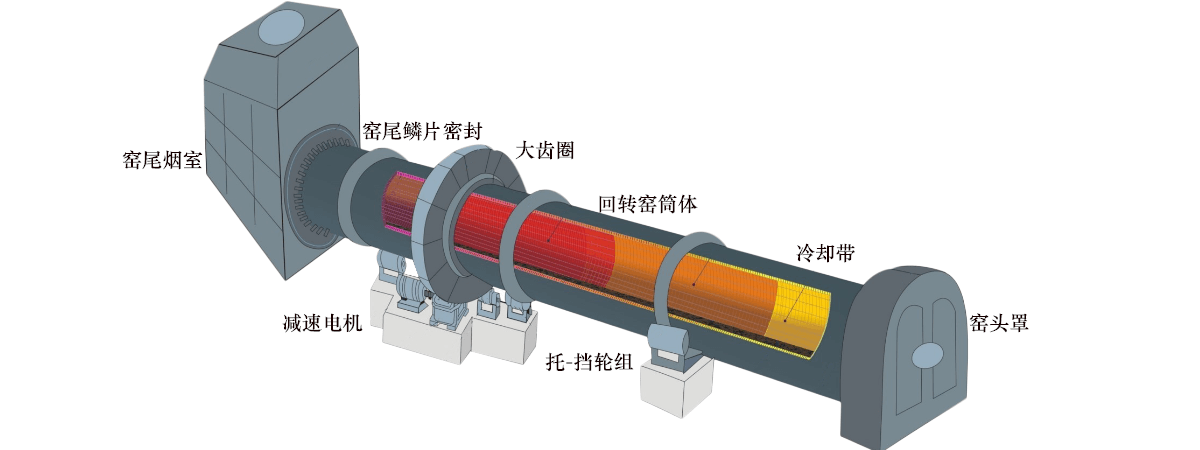
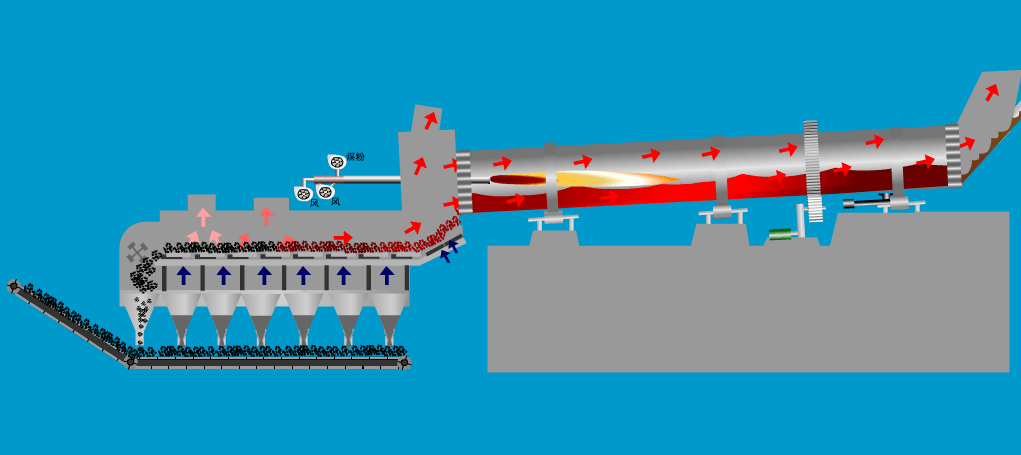
Rotary kiln includes: barrel, belt, supporting wheel, blocking wheel, sealing device, transmission device, accessory equipment
(1) rotary kiln (rotary kiln) on the one hand is a combustion equipment, in which pulverized coal combustion generates heat; It is also a heat transfer equipment. The raw material absorbs heat of the gas for calcining. In addition, sometimes the conveying equipment transfers raw materials from the feeding end to the discharging end. The fuel combustion, heat transfer and raw material movement must be reasonably coordinated, so that the heat generated by fuel combustion can be transferred to the raw material in time when the raw material passes through the rotary kiln (rotary kiln), which has reached the goal of high yield, high quality and low consumption.
(2) the movement of raw material particles in rotary kiln is quite complicated. If the raw material particles on the kiln wall and the raw materials inside the layer without sliding phenomenon, raw material movement is often thought to be like this: raw materials under the action of friction, as a whole with the kiln wall rises slowly, when transferred to a certain height, the raw material layer surface and the horizontal plane Angle is equal to the Angle of the accumulation of raw materials, raw materials particles under the action of gravity, slipped along the bed. As the rotary kiln (rotary kiln) has a certain inclination, and as the raw material particles roll, they fall along the maximum inclination direction, so they move forward a certain distance.
When the raw material moves in the kiln, the movement mode of raw material particles changes periodically, or they are buried in the material layer and move upward with the kiln, or they fall down on the surface of the material layer. But only when the material particles fall along the surface layer, it can go along the direction of the kiln.
The movement of raw materials in the kiln will affect the residence time of raw materials in the kiln (i.e. the heating time of raw materials). The filling coefficient of raw materials in the kiln (i.e. the heating area of raw materials); The material size turnover also affects the uniformity of the raw material (that is, the surface temperature of combustion products and raw materials).
Attention must be paid to the effects of various motion conditions on the center Angle, that is, the filling coefficient of raw material particles. If a certain filling coefficient is to be maintained in the kiln, the speed of kiln and feeding speed should be coordinated and kept in a certain proportion. This is also a process condition to improve yield, quality, stabilize thermal system and overcome agglomeration.
MODEL(m) |
Kiln body size |
Motor |
Weight |
Note |
||||
diameter |
length |
Tilt Angle |
Capacity |
Speed |
||||
Φ2.5×40 |
2.5 |
40 |
3.5 |
180 |
0.44-2.44 |
55 |
149.61 |
|
Φ2.5×50 |
2.5 |
50 |
3 |
200 |
0.62-1.86 |
55 |
187.37 |
|
Φ2.5×54 |
2.5 |
54 |
3.5 |
280 |
0.48-1.45 |
55 |
196.29 |
Kiln outside the decomposition |
Φ2.7×42 |
2.7 |
42 |
3.5 |
320 |
0.10-1.52 |
55 |
198.5 |
------ |
Φ2.8×44 |
2.8 |
44 |
3.5 |
450 |
0.437-2.18 |
55 |
201.58 |
Kiln outside the decomposition |
Φ3.0×45 |
3 |
45 |
3.5 |
500 |
0.5-2.47 |
75 |
201.94 |
------ |
Φ3.0×48 |
3 |
48 |
3.5 |
700 |
0.6-3.48 |
100 |
237 |
Kiln outside the decomposition |
Φ3.0×60 |
3 |
60 |
4 |
800 |
0.3-2 |
100 |
310 |
------ |
Φ3.2×50 |
3.5 |
50 |
4 |
1000 |
0.6-3 |
125 |
278 |
Kiln outside the decomposition |
Φ3.3×52 |
3.3 |
52 |
3.5 |
1300 |
0.266-2.66 |
125 |
283 |
Preheating decomposing kiln |
Φ3.5×54 |
3.5 |
54 |
3.5 |
1500 |
0.55-3.4 |
220 |
363 |
Preheating decomposing kiln |
Φ3.6×70 |
3.6 |
70 |
3.5 |
1800 |
0.25-1.25 |
125 |
419 |
Waste heat power kiln |
Φ4.0×56 |
4 |
56 |
4 |
2300 |
0.41-4.07 |
315 |
456 |
|
Φ4.0×60 |
4 |
60 |
3.5 |
2500 |
0.396-3.96 |
315 |
510 |
Preheating decomposing kiln |
Φ4.2×60 |
4.2 |
60 |
4 |
2750 |
0.41-4.07 |
375 |
633 |
Preheating decomposing kiln |
Φ4.3×60 |
4.3 |
60 |
3.5 |
3200 |
0.396-3.96 |
375 |
583 |
Preheating decomposing kiln |
Φ4.5×66 |
4.5 |
66 |
3.5 |
4000 |
0.41-4.1 |
560 |
710.4 |
Preheating decomposing kiln |
Φ4.7×74 |
4.7 |
74 |
4 |
4500 |
0.35-4 |
630 |
849 |
Preheating decomposing kiln |
Φ4.8×74 |
4.8 |
74 |
4 |
5000 |
0.396-3.96 |
630 |
899 |
Preheating decomposing kiln |
Φ5.0×74 |
5 |
74 |
4 |
6000 |
0.35-4 |
710 |
944 |
Preheating decomposing kiln |
Φ5.6×87 |
5.6 |
87 |
4 |
8000 |
Max4.23 |
800 |
1265 |
Preheating decomposing kiln |
Φ6.0×95 |
6 |
95 |
4 |
10000 |
Max5 |
950×2 |
1659 |
Preheating decomposing kiln |
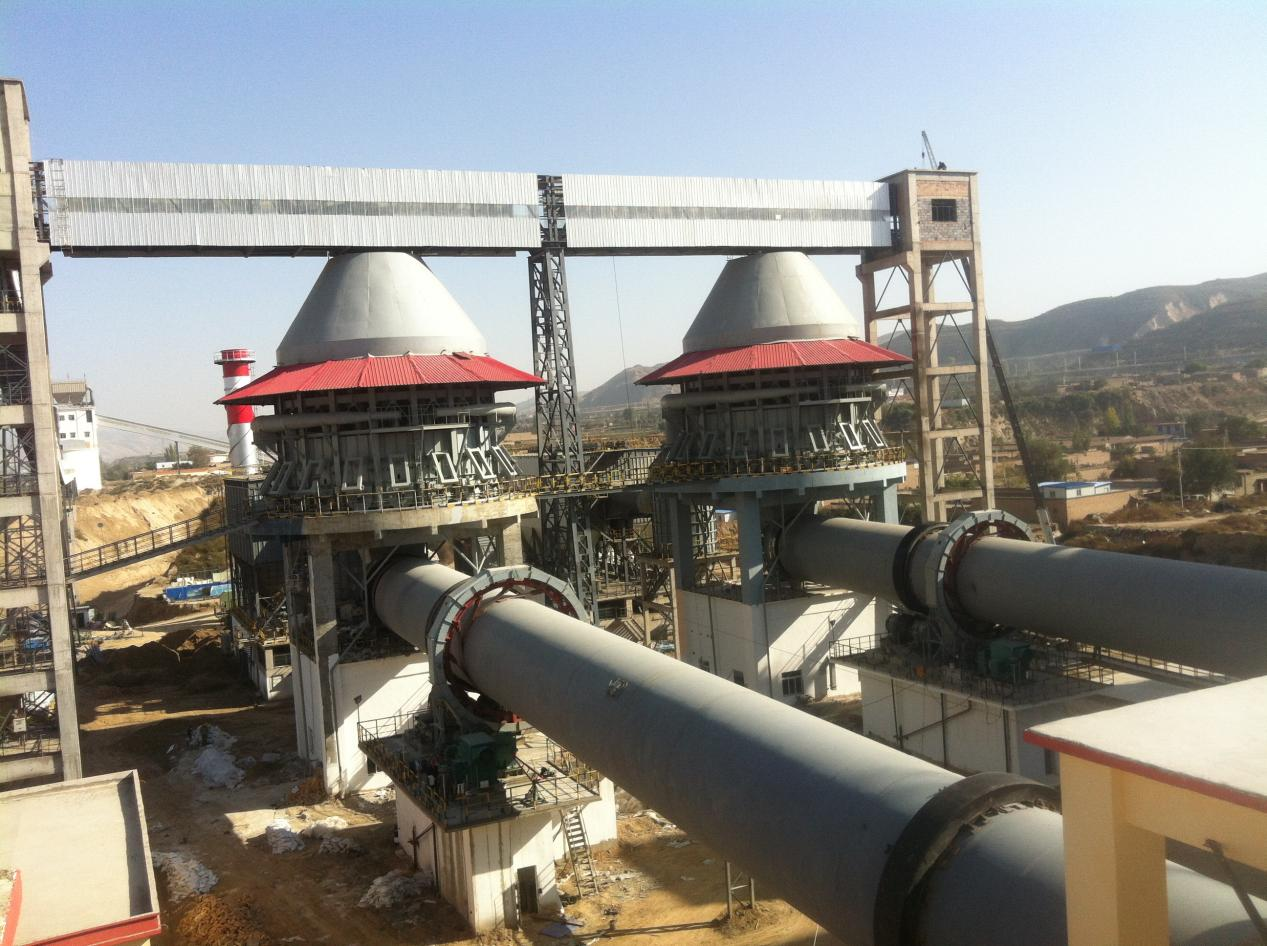
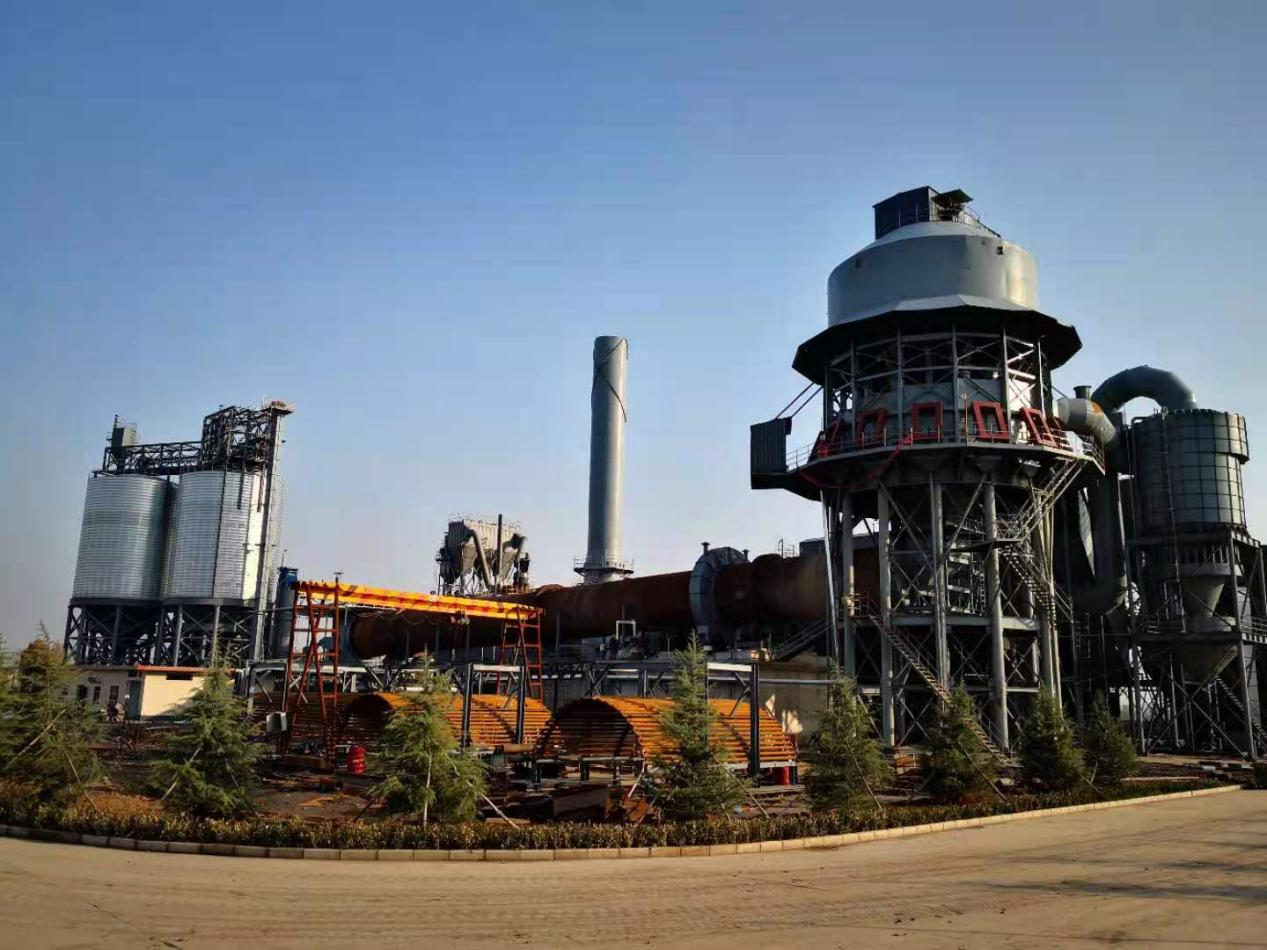
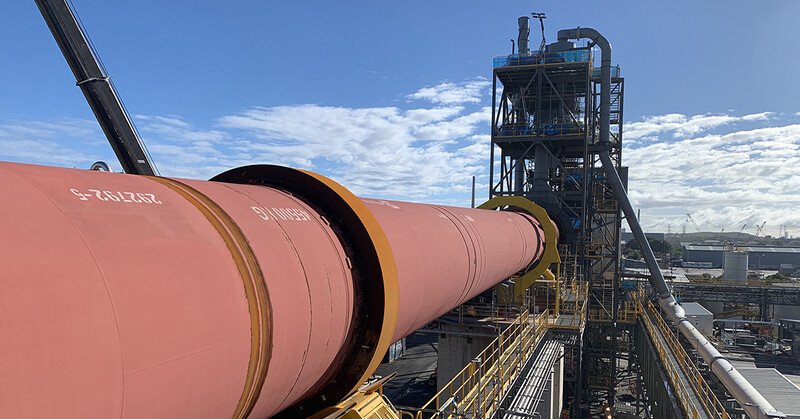
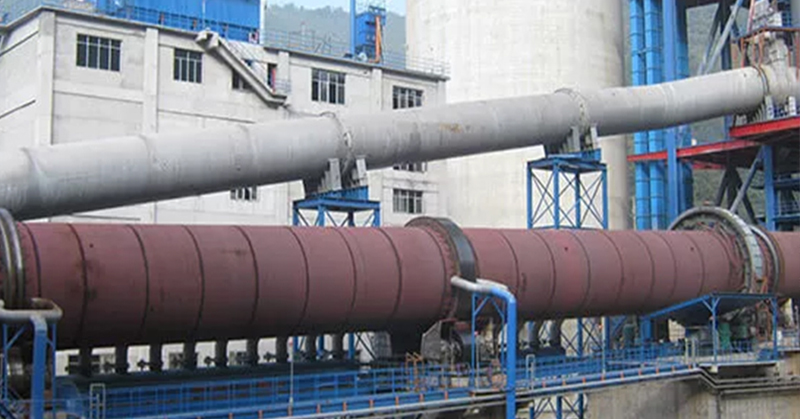
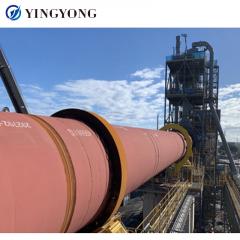
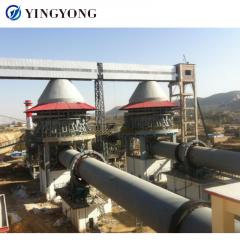
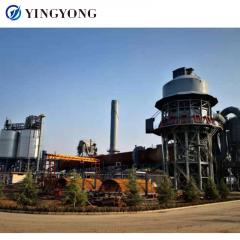